Coagulation in water treatment
Coagulation is a critical component of water treatment. In order to meet drinking water quality criteria, suspended and dissolved impurities such as silt, algae and organic matter must be removed. This is usually achieved by processes such as clarification, where colloidal particles are settled, and removed by sedimentation or filtration. Clarification requires a coagulation and flocculation process to allow small, suspended particles to floc together thus becoming larger, settling more rapidly.
Determining the optimal coagulant dose is critical, as insufficient dosing results in poor-quality treated water while too high dosing rates mean higher chemical costs and potential health risks. This is particularly true where alum is used as the coagulant as it can potentially lead to high levels of residual aluminium.
Traditionally, the optimum coagulant dose is determined by jar testing, a technique simulating coagulation and flocculation processes in the laboratory, with the optimum chemical dose identified then applied to the actual plant. It is a time and cost intensive process which requires testing various amounts of chemical experimentally. The process does not consider the rapid changes in the plant conditions and cannot provide an appropriate response to changes in raw water quality in real time, making it difficult to use for real-time control.
Harnessing the power of machine learning and deterministic modelling
The limitations of jar testing can be overcome by incorporating machine learning and process modelling using raw water quality and process control parameters (coagulant dose) as inputs and outputs.
The use of data-driven artificial neural networks (ANNs) has proven to be an effective and efficient solution to predict the required dosing to achieve the desired treated water quality.
Envirosuite’s Plant Optimiser incorporates machine learning and deterministic models based on sample and real-time data to make predictions that allow operators to better respond to variations of water quality during normal and abnormal operating conditions.
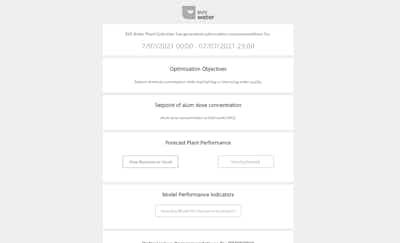
The digital twin software interprets complex process information, forecasts treatment plant performance and provides real-time advice to operators and decision makers to maintain compliance and drive performance improvements.
Using deterministic modelling methods, Plant Optimiser speeds up the setup time to a few weeks, while machine learning delivers simultaneous forecasting of alternative operating scenarios that can be used to identify operational savings.
Machine learning-based forecasts also flag potential deviation in advance of the occurrence, enabling preventative action to take place. Over time, the repetitive neural network responds and improves, thus ensuring that forecasts remain accurate and useful for decision-making, even as the water quality changes. Thus, by working in real time with data collected Plant Optimiser provides advice on the optimal dosing strategy to achieve water quality despite fluctuations in feed water quality.
Plant Optimiser sends hourly email advice on business as usual and optimised performance to help operators adjust their dosing hour by hour, without the need of doing regular time and resource consuming jar-testing.
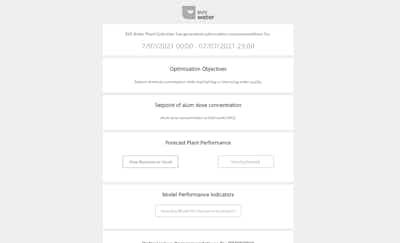
Improving operational efficiency and optimising costs at Tseung Kwan O Desalination Plant in Hong Kong
The Water Supplies Department of Hong Kong is building a desalination plant at Tseung Kwan O which will produce potable water with an initial capacity of 135 million litres per day to provide a secure freshwater resource. Envirosuite’s Plant Optimiser is currently being used to simulate scenarios with different feed water quality such as when equipment is outside of operating envelopes, chemical dosing rates, backwashing intervals for filtration equipment, and RO system flow management are optimised to provide the most efficient and lower risk operation. Plant Optimiser is used for operator training by simulating a range of scenarios for operators to manage so that they better understand and become more comfortable with managing extreme events.
In addition to providing real-time solutions around abnormal conditions and unpredicted events or other changes in water quality parameters, Plant Optimiser outputs deliver compliant and efficient operating solutions by optimising chemical and energy costs thus providing tangible operating cost benefits and confidence in risk management outcomes.